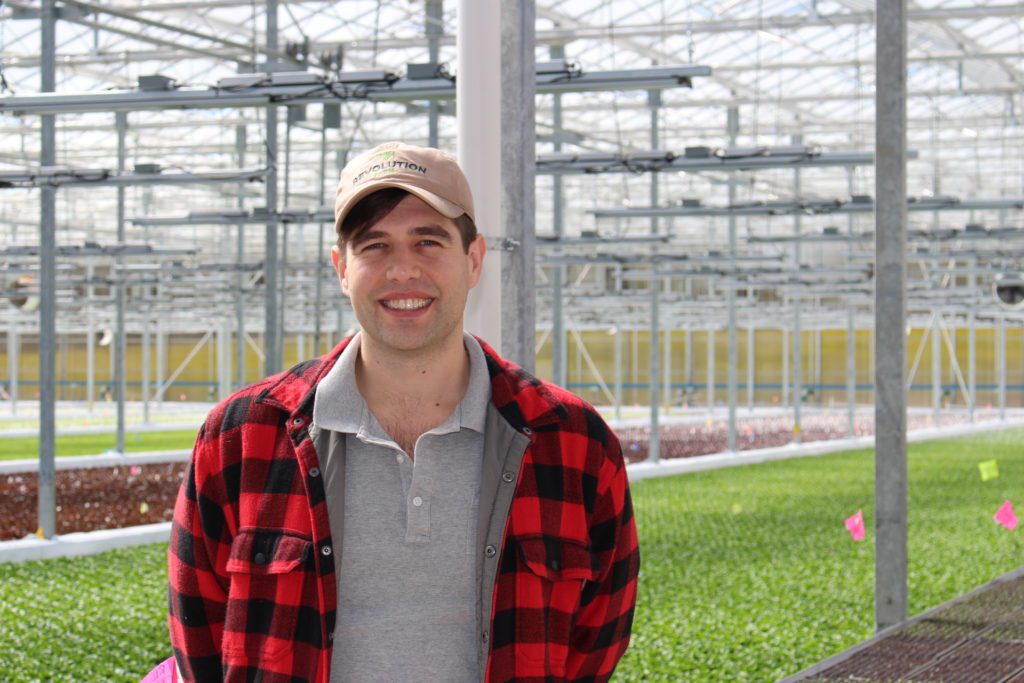
Jul 17, 2019Revolution Farms reforms practices to stay strong
Revolution Farms is showing how dynamic a startup growing operation can be in order to meet its goals.
The farm in Caledonia, Michigan, harvested its first greens in October 2018, and growers say the greens are being well-received. Originally conceived, built and operated as an aquaponics operation, in the summer of 2019 the business replaced the fish with other organic fertilizer. Even so, the leafy greens continue to flourish in the expansive new greenhouse.
Photo gallery: Revolution Farms visit
The growing operation consists of about one acre of indoor space for growing greens and a cold packing facility. The operation employs about 20 people and produces about 350,000-450,000 pounds of produce per year.
In the case of Revolution Farms, a local group of investors came together to finance the startup in west Michigan’s Caledonia.
“They all have a lot of experience building companies, and I think they want to get into a space where they could do good by doing well,” grower and senior product manager Benjamin Kant said of the investors. “This is a rapidly developing industry, obviously, and they wanted to be first-movers.”
Moving parts
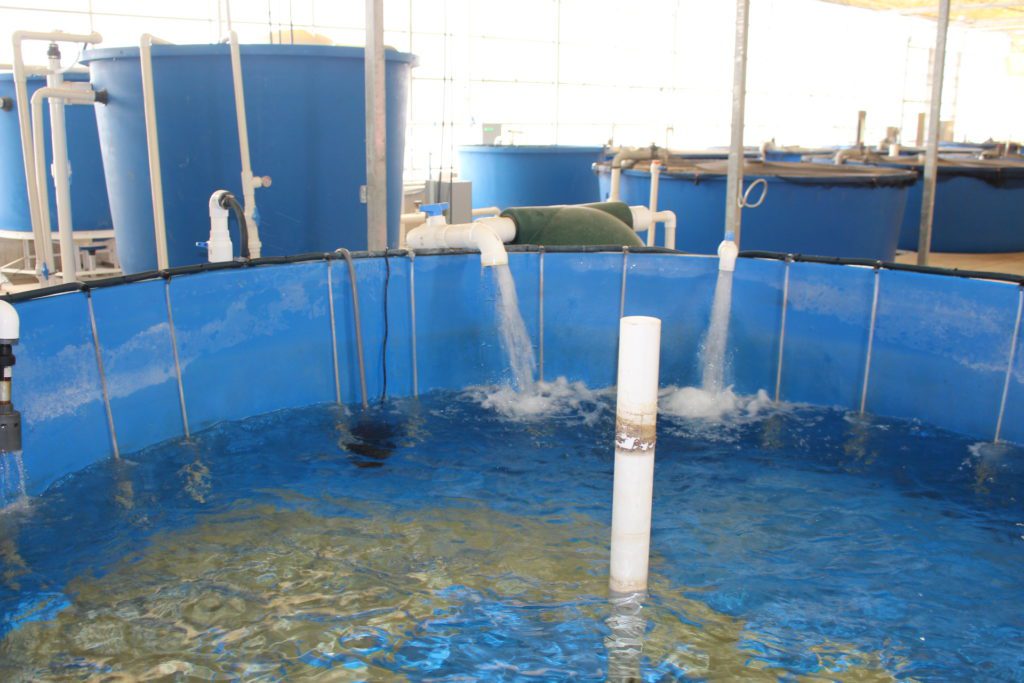
With a 50,000-square-foot greenhouse or about an acre of lettuce in a continual state of production, Revolution Farms was at the time of its launch among the largest aquaponics operations in the U.S.
The fish, omnivorous tilapia that need little protein in their diet, were raised in six wire-covered, bubbling tanks. Revolution Farms had an agreement for distributing the harvested fish, but Kant said, for the most part, they were just a good source of organic fertilizer for the greens.
In June, the company decided it could find a more consistent source for that fertilizer. Spokeswoman Erin Cataldo said the fish weren’t consistent enough, the aquaponics system couldn’t be fine-tuned, and the facility would be transitioning from an aquaponics operation.
At the Caledonia facility, the plants are raised from seeds into plugs that rest in reusable rafts. The rafts float in a deep-water culture system, long troughs that run the length of the greenhouse. The greens send bare, spindly roots into the water. During Revolution Farm’s constant state of production, new plants go in the far end of the greenhouse, and rafts full of leaves are pulled at the end that adjoins the packing facility. Rafts of whole plants, roots and all, are pulled from the water surface and placed on roller tables conveying them into the processing/packing facility.
How they grow it
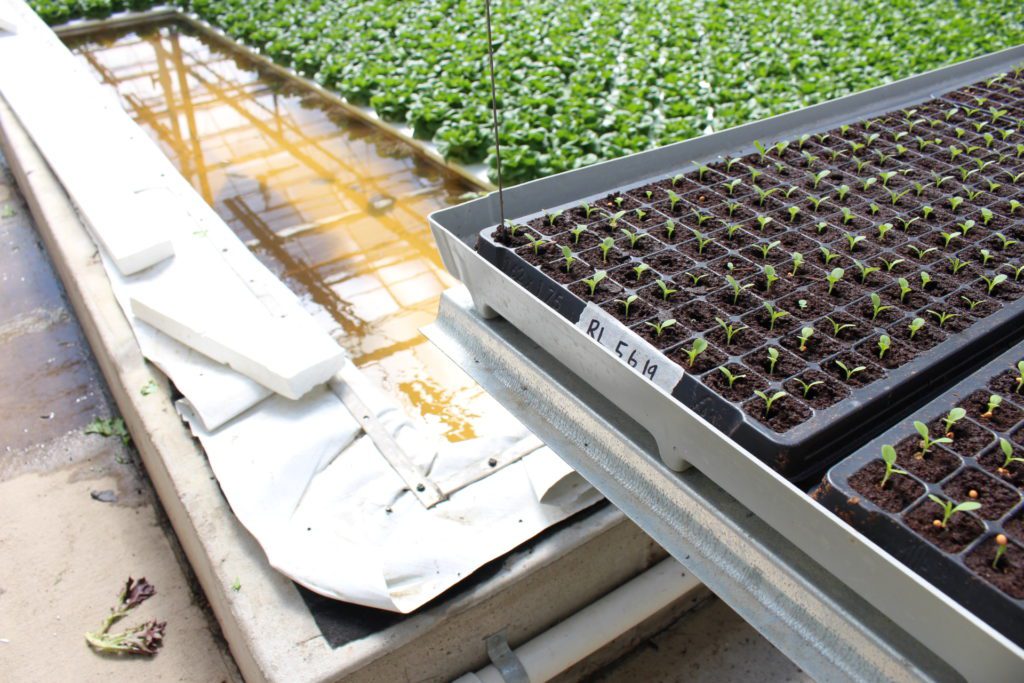
The greenhouse has side and ceiling vents as well as supplemental LED lighting. Water lost to the plants (transpiration) and the air (evaporation) is replaced.
The LED light spectra are tailored to the life stage of the plants – young plants, for instance, are fed mostly red light. The LED lamps flick on when a sensor determines the natural light has dropped. A computer program controls the greenhouse vents, and Kant adjusts the program frequently.
“We’re not to the point of a thinking computer that will adjust its parameters based on what’s going on in the environment,” Kant said.
The farm operation was set up to reach organic growing standards. Many pests are excluded by the very nature of closed-environment agriculture. Others are targeted with several different types of beneficial insects – one example is using cucumber mites to control thrips. All other control products Revolution uses are certified by the Organic Materials Review Institute.
“It leaves the organic certification very available to us, and that’s something we’re pursuing,” Kant said.
The end products
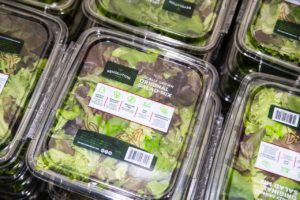
Revolution grows red oak, green oak, bibb, romaine and Sweet Crisp lettuces that are packaged into four different retail stock keeping units, or SKUs. Kant said the farm is experimenting with other crops and mixes. The products are exclusive to the grocery store chain SpartanNash, where they’re available in about 100 of the chain’s Michigan stores and a few other stores that use SpartanNash distribution.
Revolution Farms was built so that greens grow from seed to leaves and are chilled and packed at the same site – a simple setup that keeps most of the cold chain at one address.
“We’re actually only a few miles down the road from the Spartan distribution center,” Kant said. “They’ll come and pick up and the product can be on the self within 24 hours.”
As a local greens grower, Revolution’s greens products are easy for retailers to track in a time when romaine-linked disease outbreaks have made traceability a virtue.
“We found that there was a lot of demand for our product when that happened,” Kant said, referring to the outbreaks of 2018. “People really want transparency. They want to know where their food is coming from, and that’s a story we can tell them.”
– Stephen Kloosterman, associate editor
Above, Benjamin Kant is Revolution Farms’ grower and senior product manager. Photos: Stephen Kloosterman